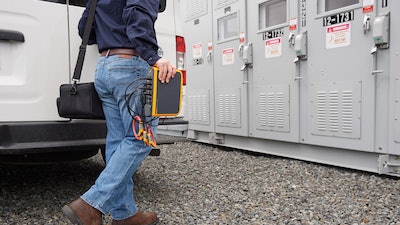
The top concern for industrial plant managers is downtime, which really comes down to cost. The cost could be in the form of equipment damage, the process not being able to function properly, or the plant just being down and not operating at all, which could be a huge loss financially. This is the central play for predictive maintenance programs, to help reduce or eliminate completely the issues that cause these types of financial losses.
There are two lines of thought when it comes to power quality investigations: look to the power and look to the equipment.
A Look at the Power
When it comes to power quality, you might assume the origin of the problem is emanating from the utility when it is much more likely to have started within the facility. In fact, many power quality tools base their power standard on the incoming power (EN50160 for Utility Power Distribution). What this means is that the data you collect in your power quality tool is compared to incoming, clean power from the utility. Power quality measurement tools should be rated to EN50160 so they can measure at the service entrance to capture incoming utility power.
A Look at the Equipment
Equipment has failed, so start asking questions. Your best bet is to bring along an engineer, electrician, or operator and interface with people on the plant floor. Here are some starter questions. Note that the responses to these questions might lead to more questions that get you closer to understanding the origin of the failure.
- Was the device up and running properly before the event?
- When did the event occur?
- Have you seen the device behave like this before?
- What was the weather like at the time of the event?
Collect as many details as possible. Establish a time weather table that shows when the events are happening and what the weather conditions are like. You might need to identify whether the issues are widespread.
- Is the issue limited to the equipment?
- Is this a whole-plant issue?
- Are my neighbors experiencing similar issues?
Keeping a detailed record of the events, as well as when and where they are occurring, will help you decide on the best approach to capturing power quality data.
Capture Power Quality Data
There are two approaches to capturing power quality data. The first is best for predictive maintenance and involves the use of a power quality monitor or power quality recorder. The data collected using these types of tools can be used to build a baseline for the equipment and or plant. These measurements are taken over longer periods of time (up to months) meaning that the data will include a multitude of operations scenarios, such as varying capacity levels, large equipment startups, and equipment shutdowns for maintenance, which can impact power quality in a large facility.
Taking power quality measurements using a Fluke 1730 PQ Analyzer.Fluke Corporation
The second approach is for troubleshooting and involves the use of a power quality analyzer for data collection. While you might not be the individual responsible for evaluating the data, you need to use the right tool to collect the data. The higher the sophistication, the higher the speed events (such as transients) the tool will be able to collect.
Not knowing what the event is, the power quality analyzer will allow you to not only look at instantaneous data but to also capture historic information can be used for trending and record keeping. It’s not enough to know that an event occurred. You need to keep a record of when it occurred. You need to establish a timeline. In power quality, a timeline can indicate trends that go beyond the numbers. Are there any correlations between the events and other things that are going on in the facility? With the weather? This is the primary starting point to figuring out exactly where the problem is coming from.
Voltage Sag Events
The number one complaint within a facility is voltage sag, or a drop in voltage and they can occur for multiple reasons. Voltage sags effect devices that run off electric power supplies, such as electronic switching power supplies that only draw on the positive portion of the cycle. When deprived of the voltage, the power supplies might not work properly and ultimately cause electronic equipment failures. The issues could be seen in personal computers, drive trips on variable speed drives due to low DC bus voltage. You might see issues with lighting ballasts, such as flickering.
- Large loads are the most common reason for voltage sags and in a large facility, large loads are coming from everywhere. Motors, woodchippers, rock crushers—all of these are large loads that once powered up can create a drop in voltage.
- Depending on how your power grid is set up, weather conditions might be a contributing factor, including wind, lightning, excessive heat. Hot conditions can cause power quality issues with transformers, for example.
- Short circuits in the system will cause voltage drops.
- Loose connections will cause a permanent or intermittent increase in impedance. (Note that loose connections in a panel can be easily and safely diagnosed with a thermal imager.)
Loose connections in a panel can be easily and safely diagnosed with a thermal imager.Fluke Corporation
Solving for Voltage Sag
There are multiple ways to deal with voltage sags, but ultimately it depends on the needs of the facility and the maintenance level the team is willing to allow for in their predictive maintenance program.
- A UPS can handle long voltage sags but are often the more expensive option and have associated maintenance costs.
- Using both a UPS and external battery banks will allow for the system to ride through longer sags and even voltage outages.
- A SAG compensator is more of a passive solution that isn't designed for long-term fixes. Instead, it will ride through about 250 milliseconds of time for a voltage sag or outage. In that time, that would be about 3 to 15 cycles (at 60 Hz, one cycle is 16.67 ms). The SAG compensator is the least expensive option.
- A rotary diesel UPS require a lot of space and can be very expensive. They are basically a diesel motor and will consume more energy. In addition, they need regular maintenance. Rotary diesel UPS systems are not as commonly used because of the associated costs to run and maintain them.
- Another approach is a motor soft start, which helps reduce inrush current which causes voltage sags. Even a variable speed drive would allow a motor to be started in a slow manner to reduce inrush current and thus the sag.
- Electronic voltage regulators or tap changers are like transformers where you can switch taps to automatically change the voltage level. This is another somewhat expensive option and it is less efficient.
Jason Axelson is a power quality expert for Fluke Corporation.