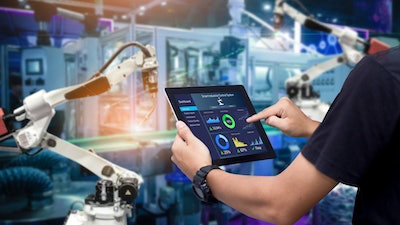
The recent inclusion of artificial intelligence and machine learning to power robotics within the workplace has jettisoned productivity to new levels of performance. Up until recently, robots handled jobs that we call the 4Ds – dirty, dangerous, dear, and dull. But the recent introduction of collaborative robots (cobots), meant to operate closely with humans to perform their tasks, has increased productivity while reducing employee costs.
The idea behind cobots is to augment human actions, making workers and their jobs more effective. One of the most compelling stories featuring cobots today is the Oregon-based company Darex, which manufactures drill and knife sharpening equipment. As new orders started to bottleneck assembly lines, Darex purchased cobots to help with automated screw driving and box building, both of which are less-desirable tasks for workers. Overall, Darex witnessed a 27% performance improvement while helping with redeployment of employees to more valued areas of the business. There are so many expanded opportunities with cobots beyond robot-assisted assembly, that the future of cobots looks promising. In fact, according to a Global Collective Robot Market study, the cobot market value will reach $9.13 billion by 2024, a 58.79% year-over-year growth rate since 2019.
With this new machine and human collaboration in mind, companies will need to rethink many policies – and policy management – that surround their workforces. Take Ford Motor Company for example, where cobots work with humans to assemble shock absorbers. Cobots handle the heavy weight to position the shock absorber while the human technician fastens the part into place. With this interaction, new policies for safety, care, maintenance, and powering down machinery were all introduced to ensure seamless productivity and a safe environment. Without a doubt these new policies needed to be managed in a new way.
Policy management is an overlooked resource. Using the analogy of a brick-and-mortar structure, some may think of policies as the bricks, but in fact they are the mortar. It’s the procedures that consider cultural aspects, such as over-use of power, or satisfaction and happiness at work, that hold the structure together well and result in optimal performance. Understanding this heading into the cobot era, and taking action, will increase productivity for manufacturers’ businesses.
Here are the two most important areas of policy management to consider in the human-cobot workforce era, to ensure your employees are prepared.
Acknowledgement
Unlike robots, cobots are smarter, using sophisticated programming that can be remotely controlled. They are much lighter and more agile, and generally safer to work with than their previous generation. So, when a worker accidently bumps into a machine, it results in an unfortunate incident rather than a tragic event.
Even though health and safety policies can be programmed within cobots, organizations must re-write policies for employees when entering into areas where cobots exist. It is paramount that employees acknowledge these new policies to fully comprehend the nature of their collaboration with intelligent machines. With cobots, workers are meant to get close, real close, to work in tandem.
This illuminates many new rules and regulations that workers must follow with strict agreements for their safety and for the machines to run with optimum performance.
Acknowledgement of policies means documenting employees’ understanding of them. Without computers on the factory floor, companies will need to go the extra mile to ensure that all employees have access to policy documents, regardless of the nature of the role or its location. This could mean supplying computer terminals in designated spaces, or perhaps the ability to sign laptops in and out of the plant.
Easy access for all employees will be the minimum standard, including providing an online portal for individuals to manage their own policies, with their unique log-in and profile. The key to success is to provide the means to connect to the policies that are relevant to each person specifically, relating to the job each one performs. And access will need to be available from anywhere in the world, at any given time. Most importantly, it will be absolutely necessary for you to know that each one has understood the policies agreed to.
For those manufacturers with hundreds or thousands of human employees on their factory floors, how will they ever be able to keep up with the questions that will arise? Policy authors and manufacturing personnel will need to connect through their policy portal on a forum. Having questions answered in this way empowers employees to better own their roles and their areas on the factory floor, because giving employees a way to express their voices is the most powerful thing you can do for them.
Communicating in a unified way, such as with a forum, will make re-writing policies much more digestible for policy authors, who may not know what to expect heading into policy writing for the new world of cobots. Policy authors may have no way of knowing how people will react under these new circumstances, but what they are certain of is that they will be responsible for new policies, and they will be time consuming. New mechanisms will help them adapt, using older polices to build on for enhanced documents, mostly because their work is time sensitive. Enabling policy authors to move quickly through updating many policies efficiently is a critical and often forgotten necessity of any successful policy management program.
For policy authors and factory-floor personnel alike, knowing where policies are, what’s important to know about each one, and that everyone has an understanding, will become the foundation for employees to launch into the human-cobot experience.
Dispute Resolution
In the future, the world will encounter the unknown when a machine and a human can’t connect. A machine knows nothing except for its job, which means it’s the humans who must adjust themselves to be able to work with machines. If they cannot, due to any bias demonstrated by the machine, be it an accessibility issue, or a disagreement on job completion, for example, dispute resolution between these machine workers and human workers will become critical. And it will embody a whole new meaning as we add to policy management human-to-machine policy.
Some main criticisms of cobots are generally rooted in policy management participation. For instance, rules and procedures that govern human proximity: How can the cobot choose the right course of action through different circumstances? In other words, rather than programmers just downloading the software to have cobots perform the tasks, they must upload relevant policies for safety and performance optimization. Security policies within cobots are a definite conversation topic for data protection and breaches. At what level do these machines’ firewalls secure the operating software to ensure they don’t go offline and inflict damage or harm? Finally, policy standards for speed of movement and grip strength certainly need consideration. This is the most difficult area of advancement that all cobot manufacturers are focused on improving.
The Bottom Line
The growth of cobots in manufacturing illustrates continued innovation for machine learning to make significant improvement in cost, employee satisfaction, and safety. At the core of programming, policies must be embedded within these machines along with having very clear, specific employee policies and ease of policy management. By doing so, companies will be better prepared for the unknowns that lie ahead.
Darrell Cook is President of myPolicies, an online policy management and administration software company. For more information, visit www.mypolicies.com.