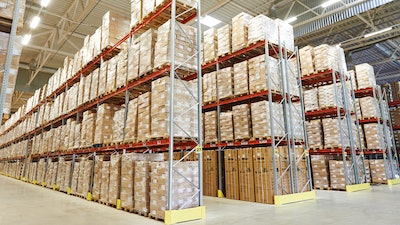
“Lights-out” operations in distribution centers and warehouses help organizations improve efficiency and reduce costs in today’s competitive business environment. In a lights-out distribution center or warehouse, there is little or no human presence, and the facility is operated entirely by automated equipment. When moving towards lights-out operations, companies tend to focus on the logistic efficiency and better end user experiences, often overlooking equipment health analytics. But even minor equipment issues can significantly reduce productivity and efficiency in a largely automated warehouse. True lights-out operations can only be achieved by introducing automated methods to monitor equipment health and reliability, ensuring that the automation equipment runs as intended without the need for unplanned human intervention.
Distribution centers and warehouses play a critical role in the supply chain and form the backbone of a company’s logistics and distribution operations. They receive, organize, identify, and store items before sending them out to shipping bays, where they are shipped to stores, customers, or other distribution centers.
Automated distribution centers already exist, with most of the manual labor being performed by robots and machinery, but tasks such as product picking, packing, and labeling are often still carried out manually. The logistics of shipping and distribution centers are typically a hybrid of manual and automatic. Current lights-out distribution systems still require a group of repair and maintenance engineers to be constantly available to deal with potential equipment failures, which prevents them from achieving true lights-out status.
Why Equipment Monitoring is Crucial?
All too frequently, companies focus on operational costs, product analytics, and equipment failure risk rather than paying close attention to the health of the equipment itself. While logistic analytics are important, ignoring equipment health comes with serious pitfalls. Equipment failures are expensive and time-consuming, both because of repair costs and productivity loss. If a piece of machinery on a car assembly line fails, for example, a parallel line must be used at a higher rate, putting the second line at higher risk until the first line can be repaired, and operational efficiency falls. In distribution centers, most of the equipment tends to be specialized, so repairing failures is especially costly.
Many companies already have systems and technologies in place to monitor automation equipment, including video analysis for size and shape complexities. These systems can be adapted to monitor equipment health as well. With equipment monitoring built into every step of the process, the automated system will be able to predict equipment failures before they happen with the help of predictive analytics, order replacement parts, and coordinate the necessary services of repair technicians well in advance. For example, a distribution center might make use of miles of conveyor lines. Repetitive motion could eventually cause the moving parts to show wear and tear. Worn-out parts often have higher surface temperatures than good parts. This change in the part’s heat signature when compared to past reference temperatures will allow the predictive analytics system to recognize there is a problem with the part and plan to order a replacement part or notify a repair technician—preparing to address the issue before a portion of the conveyor line stops functioning or breaks entirely.
Achieving True Lights-Out Operations
The difference between lights-out and true lights-out operations is the difference between reactive and proactive equipment maintenance. Rather than waiting for failure to occur and responding once it does, a true lights-out operation monitors equipment health and engages in predictive maintenance. The use of equipment health monitoring and predictive analytics reduces the need for emergency manual intervention and allows minimal teams of engineers to monitor potentially hundreds of distribution centers.
Larger companies are already devoting research and resources to true lights-out operations. Amazon’s Reliability Maintenance and Engineering wing is devoted to researching and expanding their effort towards utilizing equipment health and predictive analytics. Smaller companies are often reluctant to adopt equipment health analytics because of the higher initial costs. Yet, with improved equipment reliability and plant efficiency, they will save money in the long run by investing in these solutions.
Adding equipment health analytics to a lights-out distribution center will allow companies to achieve true lights-out operations, which will benefit their efficiency, productivity, and bottom line. By leveraging the power of data analysis and visualization techniques organizations can monitor equipment performance and condition, proactively address potential issues, improve efficiency, and enhance safety. All organizations that utilize automation equipment like distribution centers, from the automobile to the farming industry, can benefit from using equipment health analytics to move towards true lights-out operations.
Shreedhar Murthy Hebbur Subbaraju has over two decades of experience in product and systems design and manufacturing engineering. His expertise ranges from complex injection moldings to critical aero engine component development. He has an honors bachelor’s degree in mechanical engineering from Bangalore University, India. Shreedhar has served as an expert reviewer to Edison Awards. For further information, contact hsshreedhar.75@gmail.com.