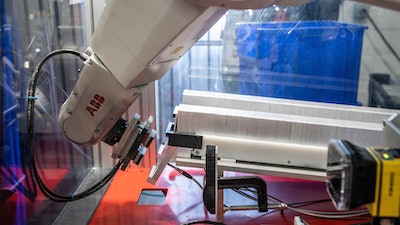
BJ Minson didn’t like the imperfect fit and sloppy profile of the standard belts he could find on the market, with the buckle and excess strap end awkwardly protruding from under his untucked shirt. So while working on a master’s degree in microfluidics, he began playing around with the design for a sleeker belt with a more precise grip.
Already equipped with a master’s degree in mechanical engineering and a keen interest in product design, what started as a diversion from his ongoing studies became a preoccupation as Minson got closer to a breakthrough design. Ready access to a laser cutter allowed for the testing of a wide range of buckle concepts, and eventually the Eureka moment came, and Minson discovered the perfect buckle and belt design: Firm fit, low profile, no holes and no strap flap.
As alluring is a career in microfluidics, Minson put that aside and founded GRIP6 (www.grip6.com), a company built on the merits of his innovative belt design. Five years later GRIP6, located in Midvale, Utah, has a seven figure annual advertising budget, and an abundant volume of its belts and accessories are sold online and in over 250 US retail locations.
Early Production
The early production was the proverbial garage-based operation, selling a few hundred belts a month. Once Minson added staff and ramped up the marketing engine, monthly volumes grew into the thousands and GRIP6 moved to a dedicated facility.The highly crafted, metal buckle is the key component of the unique belt design, and its production must be precise. The initial buckle fabricating and finishing was very labor intensive, with employees using off-the-shelf processing equipment to cut, sand and finish each piece.
An engineer Minson hired in 2016 designed some processing equipment in-house to alleviate a portion of the manual burden, and while they adequately increased throughput and minimized variable costs, each workstation was dedicated to only one buckle design.
Minson describes a pivotal point in his effort to continually improve manufacturing processes: “Our in-house team did a really good job designing equipment, but very often it was to make a specific part. We got to the point where we maxed out on that approach and needed something that would accommodate more product variety with the same quality and speed.”
ABB
Exploring Robotic Automation
Convinced that robotic automation was the proper technology to pursue, Minson and team set out to find a capable robot with advanced programming software, ideally that worked well with SOLIDWORKS, able to take a solid model and find a path along more intricate edges. After some extensive research GRIP6 found that RobotStudio, ABB’s simulation programming software, could be directly integrated with SOLIDWORKS.With RobotStudio, GRIP6 could use the same robot to handle a variety of different buckles, streamlining production and making it easier to introduce new buckle designs. Producing buckles with some sort of cutout pattern or non-uniform outside profiles became far easier, leading to more creative designs and shorter development cycles.
The simulations created in RobotStudio are virtually identical to how a robot and the ancillary system components will perform on the factory floor, allowing users to optimize the system layout to achieve the necessary robot paths with the best cycle times.
Ultimately, GRIP6 purchased an IRB 1200 robot in the latter part of 2019, and bought two more identical models approximately six months thereafter. Two of the robots are cutting belt buckles, and the third is in final testing for an application finishing the ends of belt straps.
Buckle Cutting
GRIP6 currently has seventy men’s and women’s buckle designs that vary in size, design and finish. They all have two identical parallel slots inside each vertical edge, one where the strap is attached, and one on the opposite end where the strap end is inserted to secure the desired fit.The production process begins with buckle profiles and their respective strap slots being laser cut from a large sheet of aluminum. The “blanks” are then then manually placed into a 250-unit capacity feeder cartridge, from which a robot accesses one piece at a time. The robot initiates the secondary cutting process by grabbing a buckle by the two slots, and presenting it to a stationary router installed inside a protective case. The robot moves the buckle edges around the router, equipped with a 90° countersink cutter point, beveling a 45° chamfered edge on the entire outside edge of each side of the buckle, pulling the buckle out of the machining area after completing the front side, to reorient the buckle to process the back side.
During the process the robot also does a full chamfered cut along insides of both slots, which provides the friction that holds strap length in place in the absence of holes. Once complete the buckles are put onto a conveyor that routes them to a staging area for the finishing and painting station.
To provide the highest cut quality, GRIP6 installed a Cognex camera in front of the base of each cutting robot, integrated with the robot controller.
Increased Throughput, Less Waste
With the cutting programs for each buckle SKU created in Robot Studio and downloaded to the robot controller, the robots can easily cut varying buckle models within a single production cycle.When four, 250-unit capacity feeder cartridges are loaded and staged, a single robot can run uninterrupted for nearly twelve hours, cutting approximately 83 buckles per hour. In a 24-hour period both robots combined can cut 4,000 buckles, which is 33% more than the 3,000 five production workers could do manually in the same timeframe, with far less waste.