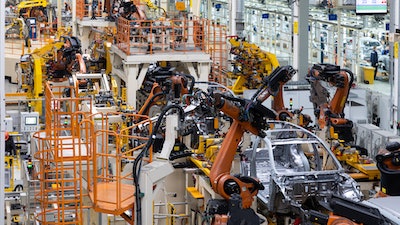
Thousands of people currently hold jobs at plants that produce gas-powered vehicles. However, S&P Global Mobility predicts sales of electric vehicles in the U.S. could reach 40% of total passenger car sales by the end of the decade.
As gas-powered vehicles are phased out, automakers must transition their workforce and infrastructure to build more electric vehicles.
Dr. Richard Kilgore, an instructor in the Online Management and Business Administration program at Maryville University, provided insight on preparing for an EV environment, possible job loss and the chance for retooling in the midst of increased reliance on automation.
Can we expect job growth, loss or about the same from the transition to EVs?
Richard Kilgore: No one knows for sure because of the uncertainty of the rate of the transition. There are macro and micro factors when discussing the economics of domestic job growth in the U.S. as we transition from internal combustion engine (ICE) to electronic vehicles (EV). For the next decade, the overarching macro factors will be:
- The total demand for EVs by U.S. consumers.
- The total amount of that demand met by domestic production facilities including those located here by non-domestic auto companies.
- The total amount of battery component demand met by domestic mining, production and battery component and assembly.
- The net amount of jobs gained or lost from the decline in gasoline fuel demand (including gas stations, refineries, distribution and oil drilling) and the increase in electric power plants and charging infrastructure.
- The impact on the supply-chain industries supporting these producers and the distribution network, maintenance and repair facilities downstream.
We can attach upward and downward arrows to many of those factors, but the size of those arrows is uncertain (e.g. There will be more EV auto design and engineering jobs and fewer ICE auto design and engineering jobs, but the net growth is uncertain based on the time period. Short term, there will be demand for both and a net increase, but long term it may be just a replacement and no new net growth).
On the micro side are factors like the impact within a production facility because of the number of components needed for final assembly. Most experts claim the EV will have fewer assembly operations and thus require fewer workers. But the larger macro factor of how many EVs will end up being supplied by domestic producers will far overwhelm how many workers will be employed at each assembly location.
And even if you had good forecasts at the macro levels, the issue of how these gains or losses would flow back through the supporting industries in repair parts, servicing and even insurance are more difficult to forecast. Yes, even the insurance industry might see a large decrease in revenue should autonomous driving and safety systems make “wrecks” a thing that only ICEs did.
So when any politician or analyst quantifies “new jobs in EVs," the tougher issue is the “old jobs lost in ICEs” and the upstream and downstream impacts in related industries. And be wary of forecasts that include the construction and engineering job growth in the new construction of new assembly plants, new battery facilities and charging infrastructure which will be enormous at first but not a sustainable job growth source as the industry returns to a steady state.
What can automakers do to prepare their workers for the EV environment?
RK: Many automakers have cited the transition to EVs as the primary reason behind recent white-collar staff reductions and predict these will continue as demand for ICEs diminishes. That is a clear message that where ICE and EV skills differ, present auto workers need to retrain themselves to be EV-capable or risk losing their positions, particularly at the staff level. Within the assembly plants, the message is less related to obtaining EV-related skills as much as it might be shift and location-flexibility.
EV automakers will want their assembly locations collocated near the battery assembly locations and they will be making a number of strategic capacity planning locations which might require workers be prepared to relocate. And it will be likely that existing production lines will experience difficult volume swings that might lead to layoffs and temporary shutdowns as it will be difficult to forecast demand and establish smooth production schedules for both increasing EV demand and decreasing ICE demand.
What people often forget is that the economics of auto production is such that there will be no long term decline to 0 on an existing ICE line. There is a volume needed to keep the facility viable that might be very near the current volume as consumer demand shifts to EVs. So workers need to be aware that business decisions to drop models and shut down facilities are often closer than they appear just as they have been for traditional ICE models that fell out of favor with consumers. The difference now is that there is not the “new ICE model” possibility of replacing the model being discontinued as often happened in the past.
How can workers with gas-powered vehicle experience prepare for the transition?
RK: The skills necessary for final assembly of an EV or ICE are not that different that a skilled and motivated assembly worker could not make the transition. And most automakers, both union and non-union, will see the benefit of offering that retraining where necessary to maintain good labor relations.
What is more likely to be a significant change for workers is the demand for ICE maintenance and repair workers. Those diagnostic and repair skills are quite different and will affect the dealer networks that have so long relied on ICE service as the primary source of dealer profit margins.
Will the increased reliance in automation for EV manufacturing make it more difficult for companies to retool?
RK: While EV manufacturing facilities do seem to be more automated than ICE facilities, this may just be a bias from the fact that most of these facilities were new production startups and had the advantage of “designing for automation.” With a blank slate design and no legacy facility, it is much easier to design automated processes so it is likely EVs will present a business case for increased automation and the reduced production cost in preparation for the eventual battle for margins as EV price competition increases. Likewise, the business case for retooling and automation in a declining volume ICE facility will be very difficult to make.