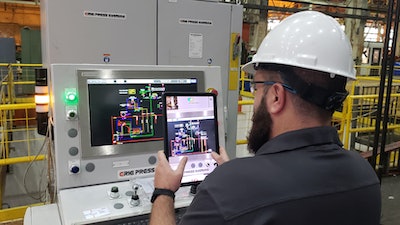
Today, forging companies face significant workforce challenges that can lead to excessive production downtime and lower productivity.
Among these are the lack of available skilled workers in manufacturing locations, the immense knowledge/talent gap left by retiring workers and the urgent need to mentor and develop younger workers.
To effectively deal with these issues, it is necessary to capture unreplaceable expertise and knowledge. Then, impart this knowledge by engaging, interactive training experiences that align with how today’s workforce prefers to learn.
As a solution, state-of-the-art Augmented Reality (AR) technology is now utilized to provide expert step-by-step forging press support and training remotely in minutes.
The new virtual tools allow forging equipment OEMs to troubleshoot and deliver problem-solving guidance to factory operations and service teams without meeting physically on site.
The approach involves real-time video communications, so both parties view the physical equipment simultaneously. AR tools also allow either party to make digital annotations on images and live video, view schematics and share documents over smartphones, tablets, PCs or AR headsets.
Using AR technology, forging equipment OEMs can accelerate problem resolution by as much as 90% and cut training time in half.
Augmented Reality technology can provide expert step-by-step forging press troubleshooting and training remotely in minutes, dramatically increasing uptime.Ajax, CECO, and Erie Press (ACE)
Optimizing Production Uptime with AR
Downtime is expensive, and if forging employees do not have the knowledge and skills to address challenges promptly, those costs can add up quickly.
Traditionally, the troubleshooting and repair of forging equipment production issues could take several days while an expert flew in to provide hands-on support.
In addition to the travel costs, this often meant the OEM’s most experienced team members were unavailable to assist others in a timely fashion while visiting or en route to another facility.
As a result, while awaiting critical assistance, forgers were often left operating below production capacity or not at all.
Today when a manufacturer requires quick resolution to forging production issues, the operator can be guided to a solution using AR technology from the largest forging equipment supplier in North America: Ajax, CECO and Erie Press (ACE).
The companies, founded in the 1800s, offer a full line of products, including standard mechanical forging presses, upset forging machines, forging rolls, wire & bar drawers, solid die forgers, trim presses, programmable die forgers and custom-engineered hydraulic presses.
ACE (a Park Ohio company) now offers ACE Vision: “Expert Connect” and “Expert Guidance” (powered by PTC’s Vuforia AR suite).
Expert Connect connects forger staff to ACE’s technical experts through an immersive AR experience to accelerate problem resolution.
Expert Guidance provides forge operator and maintenance staff with step-by-step immersive AR experiences to accelerate their productivity and learning.
Using AR technology from Ajax/CECO/Erie Press, forging equipment OEMs can accelerate problem resolution by as much as 90% and cut training time in half.Ajax, CECO, and Erie Press (ACE)
Expedited, Collaborative Troubleshooting
Innovatively, Expert Connect combines advanced AR collaboration tools with real-time video communications that are utilized to connect a forging company’s technician with an ACE expert so both can see and discuss the situation at hand.
In addition, both can draw digital annotations on a mobile screen (tablet or smartphone) or desktop that accurately stick to 3D physical objects in the real world. This allows the expert to guide a technician through a process, step-by-step.
As a result, the experts and technicians spend less time resolving issues, which increases operational productivity and efficiency. In addition, this method delivers faster resolution without the time and expense of expert travel or repeat technician visits.
An operator/maintenance technician can quickly initiate resolution with an ACE Vision Expert Connect session and then begin communicating with a press expert who will guide them through troubleshooting – often within minutes, according to Bill Goodwin, Vice President of Sales and Engineering, Ajax / CECO / Erie Press.
“If a forging machine is down, with a live [Expert Connect] session, the technical expert can see what the operator is seeing and guide them using annotations on their screen that remain fixed in a three-dimensional space exactly where drawn. This expedites problem resolution by up to 90% while helping to overcome any language barriers or issues with hearing clearly, in an industrial production setting,” said Goodwin.
Technical specialists at the forging OEM turn the forging press operation methodology into step-by-step immersive work instructions, which their employees can then engage with using a wide range of AR headsets, tablets and mobile devices.Ajax, CECO, and Erie Press (ACE)
Immersive, Step-By-Step, Professional Training
Another critical component for successful forging OEMs is operator and maintenance employee productivity, efficiency and training. In this regard, ACE Vision Expert Guidance revolutionizes the way forging employees learn, cutting time to proficiency by up to 50%.
With this approach, technical specialists at the forging OEM use an AR headset to capture the proper methodology to operate and maintain a manufacturer’s forging press.
They then turn these into step-by-step, first-person point-of-view, immersive work instructions. The forger’s employees can then engage with these work instructions using a wide range of AR headsets, tablets and mobile devices.
Today, this method is the fastest, easiest way to document and share expert employees’ years of knowledge with the broader workforce.
With Expert Guidance, ACE’s tenured experts capture step-by-step procedures and best practices as they work and then transform those insights into reusable digital process documents, job aids and training materials.
These can then be used to improve set up and changeover, streamline equipment assembly and maintenance and modernize employee training with digital, augmented reality-based work instructions.
Additionally, providing the best practices of long-time employees to the broader workforce in this fashion also helps guarantee that procedures are completed in compliance with safety standards and regulations.
“The traditional methods that manufacturers use to maintain an effective workforce are no longer sufficient and younger generations expect more engaging and immersive experiences,” added Goodwin. “So, manufacturers are increasingly partnering with forging equipment OEMs that utilize interactive AR technology.”
Goodwin notes that ACE provides standard digitized training and maintenance instructions using Expert Guidance with the equipment and can easily customize instructions should a manufacturer need anything beyond the standard.
Although manufacturers have often relied on in-person, expert OEM forging press troubleshooting and training, augmented reality technology offers a much faster, more cost-effective option.
Those who take advantage of remote, interactive, AR-based troubleshooting and training in partnership with OEMs and software providers will optimize their production uptime and operator readiness.