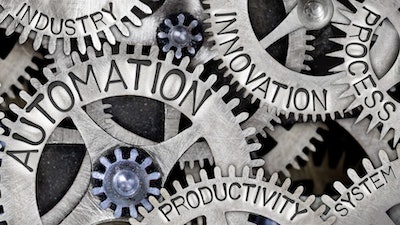
It seems like everyone in the manufacturing world is talking about digital transformation – and a lot of plant executives are rolling their eyes because it sounds like it’s disruptive, expensive and one more thing to do. In the industrial arena, where the brain trust is walking out the door every day and not being replaced, the supply chain remains challenging, cybersecurity threats creep up, and keeping profitability, quality and productivity high is job one, the very idea of digital transformation can sound overwhelming.
Let’s challenge that mindset. First, focus on three key points:
- Digital transformation is not a monolithic entity that you either have or you don’t. It’s a process, a continuum. No, you don’t have to capture the data generated by every smart sensor in the plant into a giant data lake and then figure out how to manage it. All you need to do today is determine why that one machine is producing less than the others on the line. Solve that problem, and productivity increases immediately.
- Think about the word transformation. It’s scary because it sounds like the manifesto is to “transform” the whole plant digitally. But digital transformation isn’t about digitalization or even automation. It’s about transforming the outcome of the business through the use of digitalization and automation. The transformation is in the exact goals every plant manager is trying to achieve – greater output, less waste, improved sustainability, enhanced productivity, less risk and greater profit.
- Today’s digital tools – sensors, control systems, software – have moved closer to the source of problem-solving on the plant floor. This increases flexibility and scalability so that challenges can be addressed affordably, one step at a time.
Embrace the Journey
With that in mind, let’s explore the journey an industrial manufacturing plant may take as it goes digital. While we think of plants as being high-tech, it’s actually remarkable how many processes are still recorded and reported on paper. The tracking data from clean-in-place systems in food manufacturing and pharmaceuticals, for example, is often recorded on forms by workers. Likewise, energy monitoring, a process with the promise of substantial cost savings, is frequently relegated to an inexact, time-consuming paper system.
Another example is the monitoring of compressed air on the factory floor. Meters or dials at the compressor and at various points along the production line show air pressure and air flow volume. A facilities technician walks around the plant and manually records those readings into a paper-based log sheet.
The disadvantages of a paper-based logging system are substantial:
- It consumes valuable labor time as an activity cost.
- There is a chance of manual errors in either reading or writing.
- The readings might only be taken once or twice a day so there is no insight into the performance over time.
- There is no data to support investigations into process issues such as reasons for air pressure loss.
These disadvantages in compressed air monitoring can be “transformed” through a step in the digital continuum that we’ll call digitization. The system could be digitized by installing sensors to measure air flow, pressure and volume. Data could be automatically read and logged into a database every one second to track an accurate view of the air system variables.
The advantages of a digital recording system are:
- No labor required.
- Accuracy of readings – no human error.
- Long-term data and graph trend analysis becomes available, showing any short duration peaks or dips.
- Air balance calculation can be performed in real time to identify air loss in the system.
The real transformation, however, is in the problems solved, the ability to use workforce in more profitable tasks, the improved quality and safety, and the potential cost savings. And these are all achieved in one relatively simple, cost-effective transformation in the plant.
Embracing Digital
The change from various manual work processes into a single, fully-automated process based on digital technology is the step that we’re calling digitalization.
An example could be the processes at the end of a production line. A group of people could be used to pack and seal a box of finished products, then pass the boxes down the line and stack them onto a pallet to add a final layer of wrapping. On the other hand, this end-of-line process could be fully automated with the use of conveyors, robotics, pneumatics and intelligent control systems. This integrated system combines smart conveyors, loaders, palletizers and wrapper machines. This has the advantage of working 24/7 at a speed and quality that surpasses the manual system.
Another example could be the manual process of stitching specialized medical synthetic materials to manufacture face masks. This manual process can be replaced with an intelligent ultrasonic welder that replaces the manual tasks and that melts and bonds synthetic material to produce a high-quality fabric weld.
In both examples, the digitalization, while solving a range of challenges, is a subset of the entire plant. Still, it creates substantial impact on the bottom line, with fewer workers required, greater speed and accuracy, faster time-to-market and increased output. It’s a concrete and specific transformation, making a cost/benefit analysis easy to accomplish. With today’s technology, it can also be performed with minimum disruption to existing systems and processes.
Embracing the Transformation
Because digital transformation is transformation enabled by digital technologies, each of these steps has generated transformation of the business, as well as the plant. The more a plant moves toward transformation of business outcomes, the more there’s a change to work processes across departments and/or functions. Digital transformation could also enable disruptive business models. But note, this step arrived only after the processes of digitization and digitalization are well along and already achieving transformative results.
An example of a digitally transformed process in a factory is the management of machine downtime. If a machine breaks down in the factory today, the operator might walk around the plant and look for the maintenance team. The maintenance team promises to attend to the issue when they are free, however, they may forget or get called somewhere else. The result is that production stops and no one knows when the repair will be done.
Digital tools can change the way the production and maintenance teams work together. In a digital solution, when there is a machine breakdown, the control system immediately creates a digital downtime event. The software sends a message to the maintenance team and a timer measures the time to acknowledge the breakdown and then complete the repair. Escalation messages can be sent if the issue is not acknowledged or if the downtime takes too long to repair.
The maintenance team can also then use the downtime reason information stored in the history to analyze the top reasons for machine failure. This helps them to institute new maintenance tasks or to request the production team to operate the machine differently. The workflows are transformed by the use of the digital systems.
So, the keys to understanding digital transformation are to realize it’s a continuum, focus on the exact challenges in each plant, and achieve goals and solve problems along the way. Today’s automation systems are flexible and scalable, with open communications and programming, and designed to be implemented in a step-by-step procedure with minimal impact on existing systems. Understanding this, the prospect of digital transformation becomes manageable, affordable and a way to achieve today’s goals today, rather than in some distant imaginary future.
Emerson’s Dan Coetzee is a digital transformation expert. More information can be found at www.Emerson.com/PACSystems.