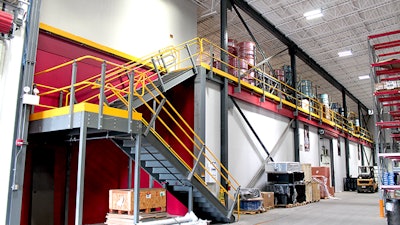
Located in Green Cove Springs, FL, Vac-Con manufactures custom-built, truck-mounted machines to serve public and private environmental markets globally. Since opening their doors in 1986, demand for the company’s high-performing products has consistently grown. To ensure success in their future growth endeavors, Vac-Con engaged an experienced architect and construction lead to manage a campus renovation project. Through a collaboration with Wildeck, a leading mezzanine manufacturer, Vac-Con was able to maximize the use of their space and create a showroom ready facility.
The Challenge
Since opening their doors in 1986, Vac-Con has manufactured more than 7,700 custom-built products for sewer cleaning, industrial vacuuming, hydro excavation and water jetting. Each year, demand for the company’s high-performing products has grown. As Vac-Con’s 300 employee owners looked to the future, the inability of the original campus to meet the company’s long-term growth goals became evident. Additional space would be needed to keep pace with the market’s growing demand.
Major renovations are frequently time-consuming and highly disruptive. To ensure that the company’s production would not be halted, Vac-Con engaged Mike Sollit, an experienced architect and construction lead, to manage the renovation project. Sollit would be responsible for creating a manufacturing environment that was lean and efficient. The new facility layout would need to incorporate areas for office space, assembly, storage, shipping and inventory. Additionally, floor personnel would need ample space to cut, weld, paint and assemble trucks. A total campus renovation was in order.
The Solution
As a fellow subsidiary of Holden Industries, Inc., Vac-Con was familiar with the benefits of a Wildeck mezzanine. They knew that their sister company’s steel work platforms created and maximized space and they wanted to incorporate the structures throughout the facility’s final design. However, Sollit had some reservations. The construction projects that he typically managed did not incorporate free-standing mezzanines. Additionally, Vac-Con’s renovation project was on an accelerated timeline. There was no room for delay.
By working together, Sollit, Vac-Con and Wildeck were able to strategically incorporate mezzanines into the campus’ final blueprints. On the shop floor, mezzanines would create accessible storage areas for individuals working in assembly, storage, shipping and inventory. A mezzanine that extended over the shop floor would also create additional office space and provide management with an elevated view of production’s daily operations.
As those in the construction industry know, preparation is crucial in determining success in the field. With over 40-years of experience, Sollit understood that the successful installation of the mezzanines would depend heavily upon his preparatory work with Wildeck. In describing this collaborative effort, Sollit said, “The Wildeck team provided me with everything that I asked for. They were highly responsive and incredible to work with.”
While discussing the mezzanine construction process, Sollit stated “The installation of the mezzanine was especially quick. I was impressed with the speed at which the platform was erected. The materials went together so easily. It looked effortless.”
Vac-Con routinely brings customers into their facility to inspect and approve trucks as part of their customer buying experience. Having their manufacturing facility showroom ready is essential to this experience. Wildeck is proud to have played an integral role in helping Vac-Con achieve their campus renovation goals.