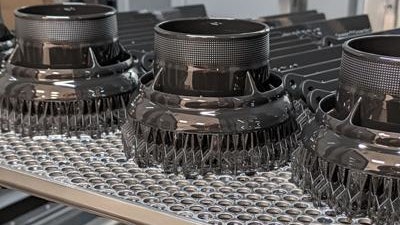
Stratasys, a provider of polymer 3D printing solutions, today announced it has completed the acquisition of the additive manufacturing materials business of Covestro AG (DAX: 1COV). The acquisition, which is immediately accretive, includes R&D facilities and activities, global development and sales teams across Europe, the U.S. and Asia, a portfolio of approximately 60 additive manufacturing materials, and an extensive IP portfolio comprised of hundreds of patents and patents pending.
The materials, IP portfolio, and talent Stratasys acquired from Covestro will help Stratasys address new applications in key technology categories such as stereolithography, P3/DLP, and powder bed fusion, including SAF technology. They complement Stratasys’ existing deep materials expertise for PolyJet and FDM technologies.
“Today marks a significant milestone for us as we solidify our leadership in the polymer additive manufacturing industry,” said Stratasys CEO Dr. Yoav Zeif. “With this acquisition, we’re not just expanding our materials portfolio for our broad array of 3D printing technologies – we’re also paving the way for more new innovations. Additionally, our growing team of in-house materials experts will be in a stronger position to collaborate with our materials ecosystem partners. Together, we’ll be able to address more applications faster, pushing the boundaries of what’s possible in additive manufacturing.”
All materials are available through Stratasys and its global partners under the Somos and Addigy brands, benefiting customers with greater global sales, service and support infrastructure. Stratasys will continue to fully support customers whether the materials are used with Stratasys or third-party 3D printers.
According to Hugo da Silva, previously Vice President of Covestro Additive Manufacturing and now Vice President of Strategy, M&A and Venturing at Stratasys, the acquisition advances Stratasys’ focus on complete solutions for specific use cases to grow 3D printing’s footprint further into manufacturing. “A new material can be as transformative to a market as a new 3D printer,” da Silva said. “Whether it’s flame, heat and smoke resistant materials for aerospace, new biocompatible materials for medical applications, or resilient materials with ESD properties for electric vehicles, we know that the more we bring new materials innovations to market as part of use case solutions, the more we can transform how everything is manufactured around the world.”