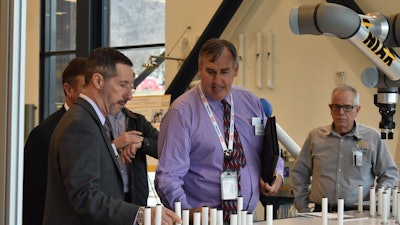
ARLINGTON, Va. — Inspecting fuel and ballast tanks. Sand-blasting old paint coatings and applying new ones. Removing corrosion on ships, submarines, aircraft and other vehicles.
These are some of the unpleasant jobs in naval shipyards and maintenance facilities that could be made safer by pairing human workers with robots. Experts say this could improve the speed and efficiency with which the U.S. Navy sustains its assets—and expand the career paths of current workers (and create new jobs) by teaching them to operate, repair and supervise robotic systems.
Robots and naval readiness took center stage at the second Joint Summit: Robotics in Sustainment—also called JROBOT—held recently at the Pittsburgh, Pennsylvania, headquarters of the Advanced Robotics for Manufacturing (ARM) Institute. ARM is a Department of the Defense (DoD)-funded consortium comprising government, industry and university partners that advances robotic technologies within the U.S. manufacturing base.
Sustainment deals with the maintenance and repair of military assets over their lifetimes.
“Sustainment is a crucial part of the National Defense Strategy,” said Paul Huang, a program officer in the Navy Manufacturing Technology Program located at the Office of Naval Research (ONR), one of JROBOT’s partner organizations. “If we can’t maintain our assets, they’re not helping our warfighters.
“One great aspect of robotic technologies is they’re dual-use and have military and civilian applications,” he continued. “The government, industry and academia have a vested interest in finding the most innovative solutions to maintenance challenges.”
The event was hosted by ARM and endorsed by both the Deputy Assistant Secretary of Defense for Material Readiness and the Office of the Secretary of Defense (OSD) for Manufacturing Technologies. During the summit, JROBOT attendees:
- Recommended OSD policy for including more robotics in sustainment. Attendees formulated policy to enable more coordinated acquisition, training and fielding of robotic systems.
- Designed new job descriptions for the 21st-century’s robotic workforce. Established an accepted set of job requirements and competencies for robotics-related work, thereby expanding the capabilities of current workers and improving recruitment and retention. Summit attendees crafted three new robotics job descriptions for delivery to the U.S. Office of Personnel Management: mechanic, operator and engineering technician.
- Selected robot projects to work in partnership with industry. During the summit, seven industry and academic partners pitched ARM-funded robotic systems they created for possible DoD acquisition. Attendees judged and selected five of them, with capabilities including underwater equipment inspection and mixed-reality software to detect defects in materials resulting from wear and tear.
“JROBOT fosters collaboration, recognizes best practices and creates shared investments in robotics,” said JROBOT co-organizer Steve McKee, who is a team lead at Naval Undersea Warfare Center Keyport Division in Washington, and oversees several sustainment projects sponsored by ONR.
Robotics can help address challenges such as aging legacy systems and maintenance facilities—and a workforce that’s shrinking due to retirements and high turnover.
“Robots are perfect for dull, dirty and dangerous jobs because they don’t get injured or suffer from job burnout or boredom,” said McKee. “By bringing more of them into our maintenance activities, and partnering them with humans, we can address sustainment needs and create a tech-savvy workforce for the 21st century. We want people who can program and operate robotic systems—not just push a button.”