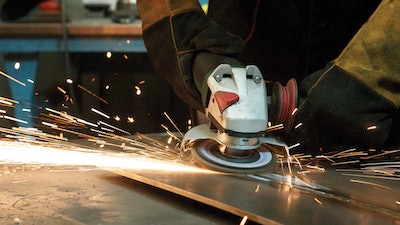
Maximizing productivity in grinding applications isn’t just about improving throughput and boosting the bottom line. Using abrasives properly also helps reduce operator strain and minimize product waste.
That is why proper technique plays such an important role in saving time and money in these applications.
How does grinding affect productivity?
The grinding operation can be a source of bottlenecks in several ways. If the wrong product is being used for the job, it can take longer than necessary to get the proper finish on the material. Choosing the incorrect product for the job can also result in added downtime due to more frequent product changeover. Too much rework can also cost time and money.
Maximizing grinding performance by using abrasives correctly creates a more efficient operator and process — which benefits the entire operation. It can help minimize rework and reduce the time spent on product changeover, too. Consider these tips to help optimize performance in grinding and get the most out of your abrasives.
Maximizing grinding performance by using abrasives correctly creates a more efficient operator and process — which benefits the entire operation.Weiler Abrasives
Storage and handling
Improper storage and handling of tools and abrasive products can be detrimental to performance, productivity and product life. Store tools and products in a cool, dry location and avoid exposure to extreme temperatures or moisture, which can cause the product to break down prematurely.
For example, humidity is the chief enemy of resin fiber disks, which can curl up if they are exposed to it for too long. Resin-bonded wheels that have been damaged or chipped should never be used because they pose a serious safety hazard.
Boosting performance
Remember, using abrasives properly helps improve performance and efficiency, and it also benefits operator comfort and eliminates waste. The end result can be significant cost savings for the operation, better productivity and a stronger bottom line.