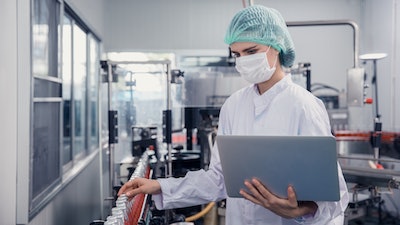
Condition monitoring is not a new concept in the food and beverage industry. It has existed in some form for decades as a means to help warn manufacturers of potential mechanical failures resulting from observed anomalies during operation. Over time, it has grown in importance and sophistication for all industries but, in the food manufacturing industry, in particular, it is especially critical due to the strict regulations and mandatory sanitation procedures that are designed to protect food quality.
Today’s condition monitoring systems are very different than their predecessors and offer significantly more capabilities than the older systems that still, today, are found in many food manufacturing plants. Although the food and beverage manufacturing sector has not traditionally been at the forefront of adopting digital trends, the improved affordability of technologies, coupled with improved software tools, make it more attractive for manufacturers to consider upgrading their systems.
So what’s new? Unlike older models, many of today’s condition monitoring solutions are wireless, run 24/7 for continuous oversight, are capable of monitoring a larger array of variables, are versatile enough to be located almost anywhere on a machine, and they are more connected to allow different systems throughout the manufacturing process to communicate with each other and automatically take corrective action. As a result, these more sophisticated monitoring systems adhere to ISO certification and are in line with the latest FDA standards.
Benefits of Newer Features
At a high level, the advanced capabilities of today’s condition monitoring systems not only improve food quality and allow manufacturers to meet the strictest health and safety standards, but they also optimize machine performance, effectively reducing costs and improving productivity by reducing unscheduled downtime.
Wireless Options
Although many manufacturing operations still have a wired system, the newer wireless models offer unparalleled benefits, especially in the food industry where equipment is often on wheels to facilitate mobility that allows for more thorough sanitation and production line reconfiguration. Eliminating wires provides greater versatility so that monitoring systems can be located anywhere throughout the plant, even in remote areas that may have previously not been monitored. There is also a cost savings, since wires don’t have to be run (installed) and maintained or, in some cases, encased in conduit to protect against harsh disinfecting chemicals.
Continuous Monitoring
Due to strict FDA guidelines, food manufacturers can’t afford to let a problem go unchecked. Temperatures and humidity levels, for example, must be maintained exactly to avoid spoilage or compromised food quality. That’s why a system that monitors 24/7, 365 days a year is critical so that a variety of data points are constantly captured to monitor the health of the machine, as well as the food being produced.
Controlling for More Variables
In many industries, the focus of condition monitoring equipment is primarily on machine life and maintenance. So variables like vibration are typically monitored. In food manufacturing, however, the impact on the quality and integrity of the end product is paramount. As a result, attention must be paid to other variables, such as temperature, humidity, pressure, ammonia levels and mold formation, among others. The relevant variables will differ by application. A meat packing operation, for instance, will have different concerns than a facility where cereal is being processed.
Greater Versatility
Advances in sensor technology and design mean that sensors can now be attached anywhere on a machine, even in the most difficult-to-reach locations, transmitting real-time measurements. Reductions in the costs of microchips also make it more affordable to install more sensors that provide complete surveillance over an entire production.
More Connected, Cloud-based IoT Solutions
Innovations like Parker’s SensoNODE™ Gold sensors and Voice of the Machine™ Cloud software transmit real-time measurements that allow data viewing 24/7 from anywhere with an internet connection. Such remote monitoring is valuable from a financial and labor perspective, especially in today’s tight labor market. Data is presented through easy-to-understand dashboards and provides notifications when measurement thresholds are exceeded. Depending on how the system is designed, it is also possible to integrate with a programmable logic controller (PLC) so that corrective action is taken automatically rather than waiting for human intervention. This quick response is essential to ensure consistent food quality.
Edge Computing
A big buzzword in condition monitoring today is edge computing, which is a distributed computing paradigm that brings computation and data storage closer to the sources of data. The result is improved response times and minimized bandwidth. In addition, it enables IoT sensors to monitor machine health with low latencies to perform analytics in real-time.
Choosing the right condition monitoring system depends on your specific application, needs and current design. Component selection, however, is only part of the challenge. Equally important is identifying a partner with the expertise and product selection to help you smartly design your system. With the right supplier, you shouldn’t need to swap out your existing computer systems. Rather, it’s possible to program legacy and new systems so that they communicate with each other to provide meaningful, real-time, actionable data that protects your entire operation.
Looking to the future, we can expect condition monitoring systems to get even smarter through machine learning, the use of digital twins, and the addition of algorithms. The incorporation of augmented reality will further reduce labor requirements and provide more in-depth data and faster response times. This will not only allow manufacturers to comply with even the strictest quality protocols, but significantly reduce downtime and related costs.
---
Marc Williams is an applications engineer who serves as IoT Market Sales Manager for Parker Hannifin.