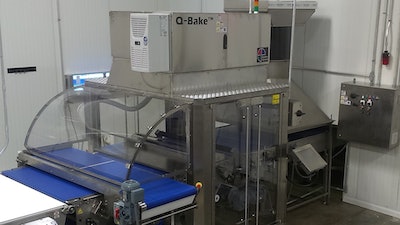
Vision inspection systems have been around for decades, helping companies improve quality and process control, and allowing them to receive 100 percent inspection of all product before packaging. Despite this, some manufacturers have been slow to adopt the technology. There are many reasons why, but the common ones are disruption of existing processes, cost and implementation.
Even though new technology may lead to more efficient production, a food producer must carefully plan implementation, navigate the changes it may cause to operating processes, and train staff to ensure the company is getting the most from their investment.
The Impact of Consumer Demand
Today, we’re seeing a rising interest in vision systems for food manufacturing, driven by consumer demand and industry trends. Vision inspection systems are comprised of a series of high-speed cameras, lasers, and imaging software to detect and measure objects and their characteristics as they move along a conveyor belt. This technology offers manufacturers the opportunity for deep insight into production processes and a more reliable method to manage product quality.
Unlike other manufacturing, such as a gear used as a machine component that should always have the same profile every time, food products vary, and many characteristics need to be measured to analyze overall quality. Consumers want a consistent product and may even be loyal to a particular brand for it.
Consumers expect consistent color, size, shape, and of course, taste. Vision systems can’t measure taste, but they are very effective at measuring visual characteristics and have even advanced to a level where they can analyze traits like crumb structure of bread products, topping placements, and custom measurements for a wide variety of food products.
Further, application-specific vision inspection solutions optimize performance for naturally variable products and ease implementation challenges by using familiar measurements and existing specifications.
Objective Data
Depending on how a company runs their manufacturing processes, often, a food producer relies on manual, visual inspection of product. Experienced and trained experts on the line can easily tell when product is out of spec due to color, size or other inconsistencies. With that knowledge, changes on the line can be implemented in order to correct major issues.
But, times have changed. These experienced staff members have moved on as part of the great resignation, and skilled labor is harder to find and keep. Vision systems help to alleviate this challenge and are giving food producers good reason to invest. They provide objective data and allow inspection on 100 percent of the products, including the bottom surface. They also help manage rejection of all of defective products and provide statistical data on the production. By automating vision inspection, companies can cope with the changing workforce.
Manufacturers can also benefit from the technology because it provides more precise detail. For example, humans may not be able to perceive slight changes in color, coating variations, and distribution of product as detailed as a machine. Their observations are subjective and may vary from worker to worker or from shift to shift.
Color variation from batch to batch may indicate a problem. Using a vision system, operators can monitor precise color and use the technology to highlight periodic trends and provide insight into problems related to specific shifts, times, days, etc.
Why Now?
Inflation. Costs are rising quickly, and manufacturers are driven to get to the root cause of quality issues and reduce waste. Vision systems provide large amounts of measurement data for analysis, and manufacturers are learning they can expand the level of quality that can be achieved and do so at full production speed. The immediate feedback about quality issues means they can be addressed much faster than before.
Vision technology improves consistency and product quality, and reduces costs in several ways:
- By providing 100 percent inspection/rejection at production speed.
- Collecting critical data and analyzing it quickly from on-line continuous monitoring and/or off-line sampling.
- With data points along your production process, alerts and feedback loops allow operators to make changes quickly and reduce waste.
Vision systems can be used to incorporate monitoring throughout the production process, as well as rejection or re-direct functionality, where the products are automatically removed from the line before packaging. This reduces waste in two ways—the manufacturer is able to view data during production and make adjustments to oven temperatures or lane balancing, for example. And there is less waste using automated rejection because the system uses objective data. This all happens at full line speed!
The data collected by these systems equips manufacturers with the information needed to make better operational decisions in their facility (not just in real-time production). Automatic reports and data analysis tools allow sites to investigate issues, look for trends, and improve their process. This contributes to successful business results.
Where to Start
Most food producers don’t jump in with large, full-scale systems at all facilities. An easy way to implement vision technology and give it a test run is to add a benchtop system to augment existing processes. This allows the manufacturer to start collecting data and evaluate the benefits a larger system can bring to their production line. And the benchtop system can be utilized even after a larger system is obtained for grab samples and quality control spot checks.
When a manufacturer is ready for a larger system, engaging a vendor specialized in application-specific vision systems for the food market is recommended. Beyond the benchtop, in-line and over-line vision systems have high throughput and can be integrated into manufacturing line controls, including rejection, redirection and laning. This takes care and proper planning.
Many times, the systems are customized for the operations and the food that is produced. Vision systems for a donut line will be different than one for a tortilla line, for example, especially when it relates to the software and measurement library. Product handling and rejection systems will also be different because of the different product features and distribution on the line. The manufacturer should always ask for a demonstration, dataset, and the vendor’s experience for an object similar to theirs at the beginning stages of the discussion.
Due to consumer demand and industry trends, finding ways to improve process control and ensure final product quality is top of mind for food manufacturers. Many are coming to the conclusion that automation will quickly ease their production challenges. And while there are some upfront costs to adding new technology, the payoff happens rapidly. Vision inspection systems result in better efficiency, reduced costs, and consistent, high quality end products—a win-win for both the manufacturer and the consumer.
Jon Gilchrist has worked with KPM Analytics since 2016, focusing on vision systems.