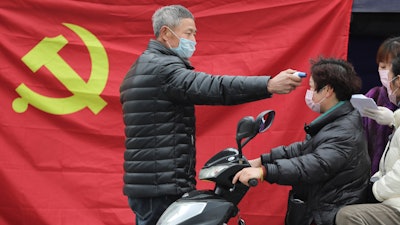
WASHINGTON (AP) — For companies bracing for losses from China’s viral outbreak, the damage has so far been delayed, thanks to a stroke of timing: The outbreak hit just when Chinese factories and many businesses were closed anyway to let workers travel home for the week-long Lunar New Year holiday .
But the respite won’t last.
If much of industrial China remains on lockdown for the next few weeks, a very real possibility, Western retailers, auto companies and manufacturers that depend on Chinese imports will start to run out of the goods they depend on.
In order to meet deadlines for summer goods, retail experts say that Chinese factories would need to start ramping up production by March 15. If Chinese factories were instead to remain idle through May 1, it would likely cripple retailers’ crucial back-to-school and fall seasons.
“There’s complete uncertainty,’’ said Steve Pasierb, CEO of the Toy Industry Association. “This could be huge if it goes on for months.’’
Wuhan, the Chinese city where the outbreak hit hardest, is a center of automotive production. It’s been closed off, along with neighboring cities, isolating more than 50 million people and bringing factories to a standstill.
So far, U.S. automakers haven't had to curb production for want of Chinese parts. But David Closs, professor emeritus at Michigan State University’s Department of Supply Chain Management, said the clock is ticking.
“I would say it’s weeks at the most,’’ Closs said. “One to two to three weeks.’’
The partial shutdown of Wuhan has already harmed the production of TV display panels and raised prices, according to a report by research group IHS Markit. The city has five factories making liquid crystal displays, known as LCDs, and organic light-emitting diodes, known as OLEDs, both of which are used for television and laptop monitors. China accounts for more than half of the global production of these display panels.
David Hsieh, an analyst at IHS Markit, said in a report that “these factories are facing shortages of both labor and key components as a result of mandates designed to limit the contagion’s spread,” leading suppliers to raise panel prices more aggressively.
Phone-maker Motorola, which has a facility in Wuhan, said that so far, it expects little impact because it has a flexible global supply chain and multiple factories around the world. Its priority has been the welfare of local employees, Motorola, which is owned by the Chinese electronics giant Lenovo, said in a statement.
Apple CEO Tim Cook told analysts last week that the company’s contractors in China had been forced to delay reopening factories that closed for the Lunar New Year holiday. Cook said the company is seeking ways to minimize supply disruptions. Some of its suppliers are in Hubei, the Chinese province at the center of the outbreak. Most of Apple’s iPhones and other devices are made in China.
In the meantime, economists are sharply downgrading the outlook for China’s economy, the world’s second-biggest. Tommy Wu and Louis Kuijs of Oxford Economics have slashed their forecast for Chinese economic growth this year from 6% to 5.4%. They expect most of the damage to be inflicted in the first three months of 2020.
“But a more serious and long-lasting impact cannot be ruled out,’’ they wrote Monday.
Forecasters are contending with unknowns. No one knows how long the outbreak will last, how much damage it will cause or how policymakers will respond to the threat.
“We’re grasping for precedents,’’ said Phil Levy, chief economist at the freight company Flexport who was an economic adviser in the administration of President George W. Bush.
Some look back to the SARS outbreak, which paralyzed the Chinese economy for the first few months of 2003. But the damage from SARS faded quickly: China was booming again by year’s end. And the world economy emerged mostly unscathed.
But times have changed in ways that are not favorable to containing the economic damage. Back then, China was the world’s workshop for cheap goods — toys and sneakers, for instance. Now, China has moved up to sophisticated machine parts and electronics like LCDs. And it accounts for about 16% of global economic output, up significantly from just 4% in 2003.
Levy said he was struck by how U.S. airlines reacted to the coronavirus: They suspended flights between the United States and mainland China for weeks — American airlines through March 27, United through March 28 and Delta until April 30.
The move doesn’t just affect tourists, students and business travelers. Passenger planes also carry a lot of freight.
“When you see them loading those big 747s, that’s not just your luggage,’’ Levy said. “That can be pallets full of electronics and other things.’’
The health crisis coincides with an especially difficult time for China’s factories. A 19-month trade war with the United States — in which the Trump administration imposed tariffs on $360 billion of Chinese imports — has already led U.S.-based multinational corporations to look for alternatives to Chinese suppliers. Many are moving to Vietnam or other low-wage countries to dodge President Donald Trump’s taxes on Chinese-made goods.
The coronavirus, along with fears that U.S.-China tensions over trade and geopolitics will persist, gives them one more reason to reduce their reliance on China. Among multinational firms, there is “increasing unease that China is starting to become quite risky,’’ said Johan Gott, an independent consultant who specializes in political risks for businesses.
But it isn't easy to completely abandon China, where specialized suppliers cluster in manufacturing centers and make it convenient for factories to obtain parts when they need them.
Basic Fun, a toy company based in Boca Raton, Florida, has sought suppliers in Vietnam and India with no luck yet. Its CEO, Jay Foreman, said he is hoping that the factories in China will resume production by early April, which he considers the best-case scenario. But he fears that any more delays could mean that the factories don’t start to ramp up production until after May 1.
The stakes are high. Basic Fun gets about 90% of its toys from China. And Foreman has been contending with the trade war and disruptive protests in Hong Kong.
The coronavirus, he said, is “just a continuation of sitting on the knife's edge ... sleeping on the bed of nails from tariffs to the riots in Hong Kong and the virus. We just can't get a break.”