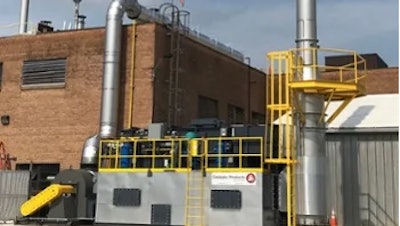
Catalytic Products International (CPI) recently installed a Regenerative Thermal Oxidizer (RTO) at a Midwest USA medical products manufacturer for the abatement of volatile organic compounds (VOC).
The 10,000 SCFM TRITON-10.95 Regenerative Thermal Oxidizer (RTO) will control VOC emissions from a single strip coating line and tunnel dryer. In this application the exhaust stream contains solvents including toluene, ethanol, ethyl acetate and methanol. The RTO destroys the VOC emissions from the coating process with 98% destruction efficiency (DRE) at a thermal efficiency of 95%.
Thermal treatment of VOCs and other air pollutants works by a simple reaction of the harmful hydrocarbon-based air pollutants with oxygen and heat. In this environment, the VOCs are chemically oxidized to form harmless inert by-products like CO2, water vapor (H2O), and usable heat. These harmless by-products are released to the atmosphere or used within primary or secondary energy recovery techniques to further lower the operational cost.
The Regenerative Thermal Oxidizer (RTO) system incorporates a ceramic media design in the regenerator (heat transfer bed) to allow thermal efficiencies up to 97%. RTOs operate by preheating the process air as it passes upward through the first ceramic heat exchange media. This pre-heated air then exits the heat exchange media and enters a combustion chamber where it is heated to the setpoint temperature and oxidization of the VOCs is completed at greater than 98% efficiency. The resultant hot, clean air stream is then passed downward through the second ceramic heat exchange media bed where it is cooled before being released to the atmosphere.
CPI worked closely with the Engineering, Procurement, and Construction (EPC) firm as well as the end user customer to design and install a regenerative thermal oxidizer to safely and effectively treat the VOC emissions from the web coating process. CPI provided a complete engineering package including ductwork design details and layout, foundation design and layout, and utility requirements. CPI fabricated and delivered a fully skid mounted, pre-piped and pre-wired RTO with the media installed, along with booster fan, exhaust stack and high VOC hot gas bypass system.
On-site and in-office support ensured compliance with the designed bid specifications and guaranteed that entire system was installed correctly, leading to a short start up and commissioning time frame.