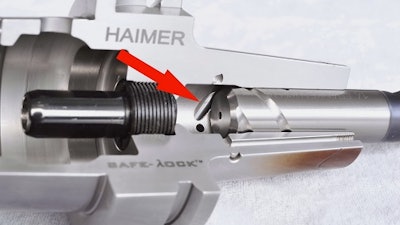
MTU Aero Engines is Germany’s leading engine manufacturer and an established global player in the industry. The company engages in the design, development, manufacturing, and support of commercial and military aircraft engines in all thrust and power categories and stationary gas turbines.
Jet engines are high-tech products. In their production, innovative technologies and processes are used. To keep current technologically, MTU develops innovative manufacturing strategies, and if necessary obtains additional external expertise.
So was the case when they contacted HAIMER, the tool holding specialists from Igenhausen, Germany, to help optimize the demanding machining process of manufacturing frames and castings.
Difficult-to-machine materials, high-quality components and the high degree of automation at MTU require an absolutely smooth and reliable machining process to maintain the highest levels of quality. In order to ensure this consistency and to control the high axial cutting forces during machining, MTU decided to implement the Safe-Lock™ pull out protection system by HAIMER.
In the HAIMER Safe-Lock system, special drive keys in the tool holder and grooves in the tool shank prevent the cutting tool from spinning during extreme machining, thus preventing tool pull out from the chuck.
In addition to the frictional clamping forces of the selected clamping system, the cutting tool is held using positive form locking in the tool holder through the constructive design of the Safe-Lock system.
Alexander Steurer, Senior Manager NC-Programming Stator Components at MTU Aero Engines AG in Munich, explains the decision for the HAIMER system, “Through the introduction of Safe-Lock and the shrinking technology from HAIMER, we can guarantee process reliability even with milling challenging high temperature materials. This is a prerequisite to guarantee smooth processing during manufacturing of frames and castings, given our high degree of automation.“
The combination of pull-out protection and highest concentricity of the Safe-Lock system leads to low vibration and as a result, a very stable machining process. Due to the increased cutting depths and feeds, the metal removal rate can be increased significantly. And thanks to the improved runout accuracy, tool life is improved by up to 50%.
The benefits of less than 3 µm runout coupled with optimum balance as well as the possibility for easy length presetting were substantial reasons for MTU to switch to the HAIMER system instead of continuing to use Whistle Notch or Weldon tooling systems. While these other systems do in fact prevent tool pull out, both are unsymmetrical by design, hence providing insufficient runout and balance accuracy.
Through the use of a set screw, the cutting tool is wedged against the opposite wall of the clamping bore. The holder pushes the cutting tool off center and thereby leads to excessive amounts of runout.
Any such design also allows for significant radial play between the tool shank and the bore itself. That way the aforementioned holders actually push the cutting tool off center, thereby inducing excessive amounts of runout.
Hans Drahtmüller, Line Manager Machining Stator Components at MTU in Munich, explains the resulting problems, “Due to the deteriorated runout, the tool life could not be fully realized. As a result, the tools with a Weldon flat had to be exchanged early. With Safe-Lock, regrinding could be automated due to the cylindrical form of the system, as the cutting tools no longer have to be inserted manually into the grinding machine compared to Weldon flat tooling. This saves tool costs."